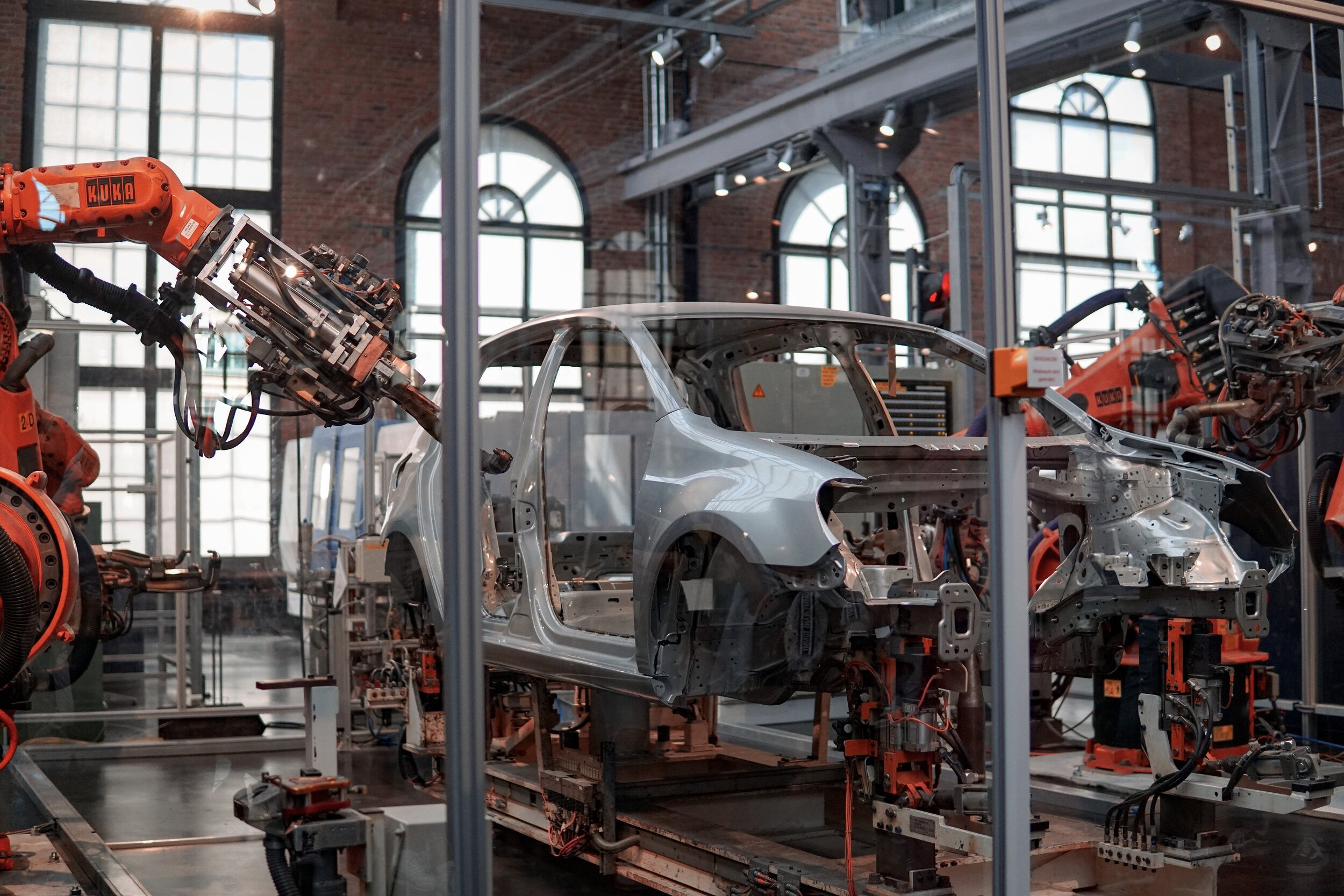
LANGUAGE OF LEAN
Cardboard Engineering
Cardboard engineering, also known as corrugated cardboard engineering, is a concept that is gaining popularity in the world of manufacturing.
Cardboard engineering, also known as corrugated cardboard engineering, is a concept that is gaining popularity in the world of manufacturing. This approach is based on the use of cardboard mock-ups, prototypes, and models to visualize, test, and improve manufacturing processes and product design.
We would like to provide an overview of cardboard engineering and its application in a manufacturing setting.
Cardboard engineering is a low-cost, fast, and efficient method for testing and refining manufacturing processes and product design. The approach is based on the use of cardboard prototypes and models to simulate the manufacturing process and identify potential challenges and limitations. This allows manufacturers to quickly test and refine their processes and products without incurring the costs and delays associated with traditional prototyping methods.
The use of cardboard engineering has several benefits in a manufacturing setting. Some of these benefits include:
Low cost: Cardboard engineering is a low-cost method for testing and refining manufacturing processes and product design. This makes it accessible to a wide range of manufacturers, regardless of size or budget.
Fast: Cardboard engineering allows manufacturers to quickly test and refine their processes and products, reducing the time required to bring new products to market.
Improved design: By using cardboard prototypes and models, manufacturers can quickly identify potential challenges and limitations in their product design and make improvements accordingly.
Improved efficiency: Cardboard engineering helps manufacturers to optimize their processes and products, leading to improved efficiency and reduced waste.
Increased collaboration: The use of cardboard prototypes and models promotes collaboration and communication between departments, improving the overall efficiency of the manufacturing process.
In order to implement cardboard engineering in a manufacturing setting, it is important to follow a structured approach. This may include the following steps:
Identify the problem: Identify the challenges and limitations in the manufacturing process or product design that need to be addressed.
Create a cardboard prototype: Create a cardboard prototype or model that simulates the manufacturing process or product design.
Test and refine: Test the cardboard prototype or model and refine the process or product design as needed.
Implement changes: Implement any changes identified during the testing and refinement process.
Continuous improvement: Continuously monitor the manufacturing process and make improvements as needed to optimize efficiency and reduce waste.
In a nutshell, cardboard engineering is a valuable tool for manufacturers looking to improve their processes and products. By using cardboard prototypes and models, manufacturers can quickly test and refine their processes and products, leading to improved efficiency, reduced waste, and increased collaboration. By following a structured approach and continuously monitoring their processes, manufacturers can ensure that they are always working to improve their operations and products
Line Balancing
Line balancing is a critical component of lean manufacturing and is a key tool for improving efficiency, reducing waste, and increasing productivity.
Line balancing is a critical component of lean manufacturing and is a key tool for improving efficiency, reducing waste, and increasing productivity. The principle of line balancing is to ensure that every workstation on a production line is working at optimal capacity and that the overall line is balanced in terms of the workload and resources available.
We would like to provide an overview of the line balancing principle and its application in a manufacturing setting.
Line balancing is a process that involves analyzing the production line and determining the ideal workload for each workstation. This is done by breaking down the tasks involved in producing a product into individual steps, and then determining the time required to complete each step. Once this has been done, the steps are assigned to workstations, taking into account the workload and resources available.
The goal of line balancing is to ensure that each workstation is working at optimal capacity, with no workstation being overworked or underutilized. This results in a more efficient production line, with less waste and reduced lead times.
There are several benefits to line balancing in a manufacturing setting. Some of these benefits include:
Increased efficiency: Line balancing helps to ensure that each workstation is working at optimal capacity, which leads to increased efficiency and reduced waste.
Reduced lead times: By ensuring that each workstation is working efficiently, line balancing can help to reduce lead times and improve delivery times.
Improved quality: Line balancing helps to ensure that each workstation is working at the appropriate pace, which can help to improve quality and reduce the risk of defects.
Increased productivity: Line balancing helps to optimize the use of resources, which can lead to increased productivity and reduced costs.
Improved work environment: Line balancing helps to create a more balanced and less stressful work environment, which can improve employee morale and reduce turnover.
In order to implement line balancing in a manufacturing setting, it is important to follow a structured approach. This may include the following steps:
Define the production line: Define the production line and identify the workstations involved in the process.
Break down the process: Break down the process into individual steps and determine the time required to complete each step.
Assign tasks to workstations: Assign tasks to workstations based on the workload and resources available.
Monitor performance: Continuously monitor performance and make adjustments as necessary to ensure that the line is balanced and working at optimal capacity.
In a nutshell, line balancing is a key tool for improving efficiency and reducing waste in a manufacturing setting. By following a structured approach and continuously monitoring performance, manufacturers can ensure that their production lines are working at optimal capacity, leading to improved efficiency, reduced lead times, and increased productivity.
Overproduction
Overproduction is one of the seven kinds of wastes in the Lean Manufacturing methodology and refers to the production of goods in excess of what is immediately required by the customer. Operations Insider - connecting the dots.
Overproduction is one of the seven kinds of wastes in the Lean Manufacturing methodology and refers to the production of goods in excess of what is immediately required by the customer. This type of waste can have a significant impact on the efficiency and profitability of a manufacturing operation, and as a Lean Management Expert, I would like to provide an overview of the negative effects of overproduction.
One of the main negative effects of overproduction is increased inventory costs. When a manufacturer produces more goods than are immediately required by the customer, the excess inventory takes up valuable space in the warehouse and incurs additional costs for storage and handling. This inventory also ties up capital that could be used elsewhere in the business, reducing the overall financial performance of the company.
Another negative effect of overproduction is increased lead time. When a manufacturer produces goods in excess of what is immediately required, the production line may become congested, leading to delays and increased lead time. This can negatively impact customer satisfaction and reduce the competitiveness of the manufacturer.
Overproduction can also lead to increased defects and decreased quality. When a manufacturer produces more goods than are immediately required, the pressure to maintain production speed and volume can lead to shortcuts being taken and decreased attention to detail. This can result in an increase in defects and a decrease in overall product quality, leading to customer complaints and reduced customer loyalty.
Finally, overproduction can contribute to a lack of flexibility and responsiveness. When a manufacturer produces more goods than are immediately required, they may not be able to respond quickly to changes in customer demand, leading to increased lead time and decreased customer satisfaction. This can also result in increased costs due to the need to adjust production processes and manage excess inventory.
In a nutshell, overproduction is a significant waste in the manufacturing process and can have a negative impact on efficiency, profitability, and customer satisfaction. By focusing on reducing overproduction and improving production processes, manufacturers can increase their competitiveness and improve their overall performance. We recommend that manufacturers continuously monitor their production processes and work to reduce overproduction and improve the overall efficiency of their operations
Stay Connected
Ad
We want information fast and in a nutshell. We from OI recommend Blinkist* - because it’s simply the best.
* = Affiliate Link