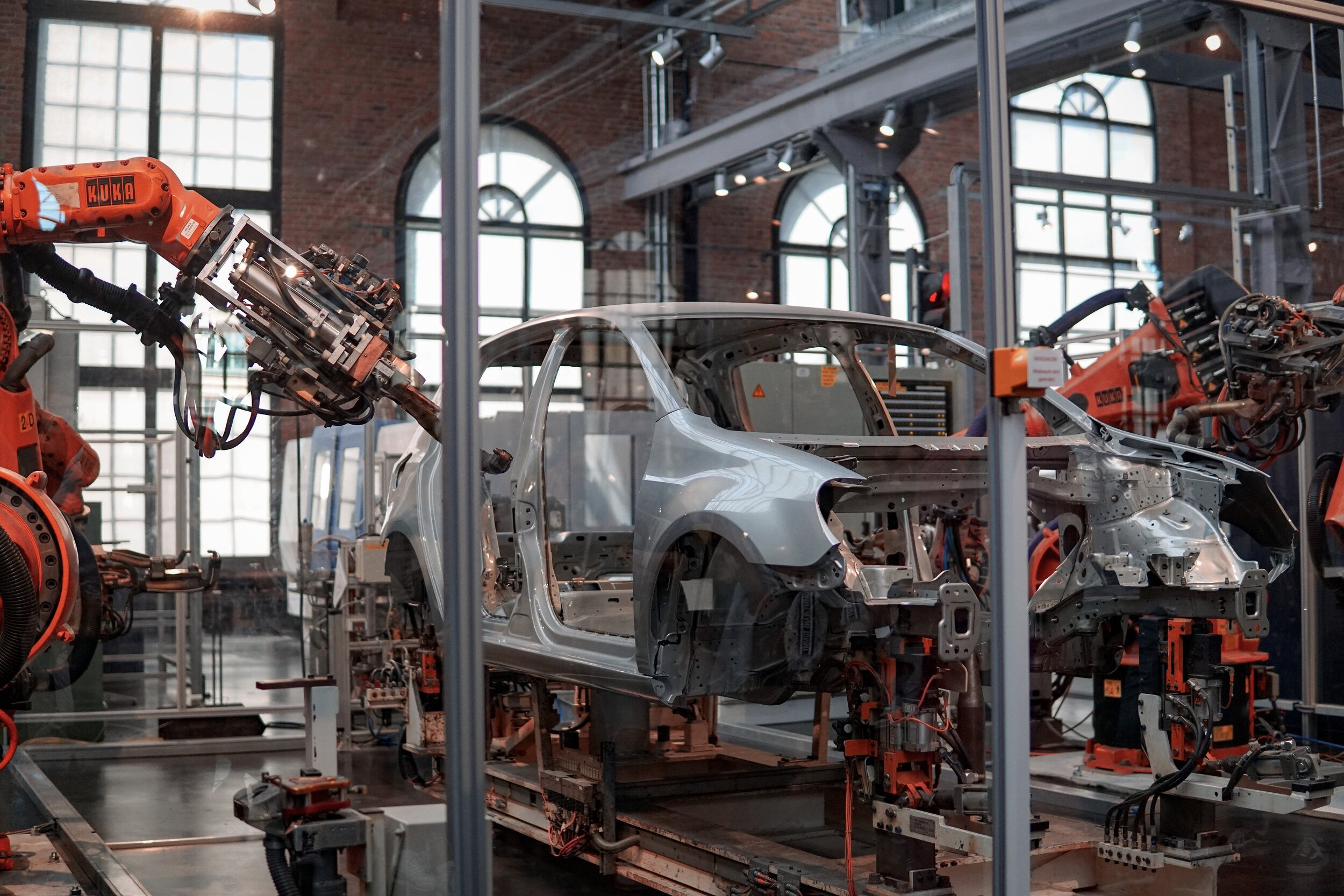
LANGUAGE OF LEAN
NVA
Non-Value Adding (NVA) activities in the manufacturing industry can significantly impact the overall efficiency and profitability of a company.
Non-Value Adding (NVA) activities in the manufacturing industry can significantly impact the overall efficiency and profitability of a company. As an Operational Excellence/Lean Management Expert, I will explain how these activities can be reduced through a 3-step plan.
Step 1: Identification of NVA activities
The first step in reducing NVA activities is to identify them. This involves mapping out the entire manufacturing process, from raw materials to the delivery of finished products, and examining each step for activities that do not contribute value to the customer. These can range from administrative tasks to inventory management, and even some production activities that are not essential to the end product.
Step 2: Reduction of NVA activities
Once NVA activities have been identified, the next step is to reduce or eliminate them. This can be done through a combination of process optimization, technology implementation, and employee engagement. Process optimization involves re-designing the manufacturing process to remove NVA activities, while technology implementation involves incorporating automation systems to streamline operations. Employee engagement involves training and empowering employees to identify and eliminate NVA activities on their own.
Step 3: Continuous improvement
Reducing NVA activities is an ongoing process, and continuous improvement is key to maintaining efficiency and competitiveness. This requires regularly monitoring and assessing the manufacturing process to identify areas for improvement and taking corrective actions. Employee involvement is also critical in continuous improvement, as they often have the closest relationship with the process and can provide valuable insights into areas that need improvement.
In a nutshell, reducing NVA activities is an essential aspect of operational excellence and lean management. By following a 3-step plan of identification, reduction, and continuous improvement, manufacturers can significantly improve efficiency, reduce costs, and enhance the customer experience. The benefits of reducing NVA activities include increased productivity, reduced waste, improved quality, and increased competitiveness, making it a critical component of success in the manufacturing industry.
Flow Cell
One of the key principles of lean management is the flow cell principle, which is all about optimizing the flow of materials, information, and processes within a manufacturing facility.
Lean management is a production philosophy that seeks to streamline operations and eliminate waste, thereby improving efficiency and reducing costs. One of the key principles of lean management is the flow cell principle, which is all about optimizing the flow of materials, information, and processes within a manufacturing facility.
The flow cell principle is based on the idea that work should be performed in a continuous and uninterrupted flow, without any idle time or unnecessary delays. This principle is critical to achieving lean goals such as reducing lead times, improving quality, and increasing productivity. In order to implement the flow cell principle, a manufacturing facility must first identify and eliminate bottlenecks and constraints in its operations.
The flow cell principle can be applied to a variety of processes within a manufacturing facility, from raw material intake to finished product shipment. For example, in a manufacturing cell, raw materials are moved from one station to another in a continuous flow, without any stops or interruptions. Each station is designed to perform a specific task, and the flow of materials is carefully controlled to ensure that the entire process is as efficient as possible.
The flow cell principle is not just about physical movement of materials, however. It also involves the flow of information, as data must be shared in real-time across different departments and processes in order to optimize flow. A well-designed flow cell system should also include checks and balances to ensure that quality standards are met and that products are being produced to the required specifications.
Another key aspect of the flow cell principle is continuous improvement. Lean management emphasizes the importance of continuous improvement, and the flow cell principle is no exception. By constantly monitoring and analyzing the flow of materials, information, and processes, manufacturing facilities can identify areas for improvement and make the necessary changes to optimize their operations.
In conclusion, the flow cell principle is a critical component of lean management and is essential for achieving lean goals such as reducing lead times, improving quality, and increasing productivity. To fully realize the benefits of the flow cell principle, manufacturing facilities must implement it as part of a comprehensive lean management program, which includes continuous improvement, real-time data sharing, and strict quality control measures.
Cardboard Engineering
Cardboard engineering, also known as corrugated cardboard engineering, is a concept that is gaining popularity in the world of manufacturing.
Cardboard engineering, also known as corrugated cardboard engineering, is a concept that is gaining popularity in the world of manufacturing. This approach is based on the use of cardboard mock-ups, prototypes, and models to visualize, test, and improve manufacturing processes and product design.
We would like to provide an overview of cardboard engineering and its application in a manufacturing setting.
Cardboard engineering is a low-cost, fast, and efficient method for testing and refining manufacturing processes and product design. The approach is based on the use of cardboard prototypes and models to simulate the manufacturing process and identify potential challenges and limitations. This allows manufacturers to quickly test and refine their processes and products without incurring the costs and delays associated with traditional prototyping methods.
The use of cardboard engineering has several benefits in a manufacturing setting. Some of these benefits include:
Low cost: Cardboard engineering is a low-cost method for testing and refining manufacturing processes and product design. This makes it accessible to a wide range of manufacturers, regardless of size or budget.
Fast: Cardboard engineering allows manufacturers to quickly test and refine their processes and products, reducing the time required to bring new products to market.
Improved design: By using cardboard prototypes and models, manufacturers can quickly identify potential challenges and limitations in their product design and make improvements accordingly.
Improved efficiency: Cardboard engineering helps manufacturers to optimize their processes and products, leading to improved efficiency and reduced waste.
Increased collaboration: The use of cardboard prototypes and models promotes collaboration and communication between departments, improving the overall efficiency of the manufacturing process.
In order to implement cardboard engineering in a manufacturing setting, it is important to follow a structured approach. This may include the following steps:
Identify the problem: Identify the challenges and limitations in the manufacturing process or product design that need to be addressed.
Create a cardboard prototype: Create a cardboard prototype or model that simulates the manufacturing process or product design.
Test and refine: Test the cardboard prototype or model and refine the process or product design as needed.
Implement changes: Implement any changes identified during the testing and refinement process.
Continuous improvement: Continuously monitor the manufacturing process and make improvements as needed to optimize efficiency and reduce waste.
In a nutshell, cardboard engineering is a valuable tool for manufacturers looking to improve their processes and products. By using cardboard prototypes and models, manufacturers can quickly test and refine their processes and products, leading to improved efficiency, reduced waste, and increased collaboration. By following a structured approach and continuously monitoring their processes, manufacturers can ensure that they are always working to improve their operations and products
Stay Connected
Ad
We want information fast and in a nutshell. We from OI recommend Blinkist* - because it’s simply the best.
* = Affiliate Link