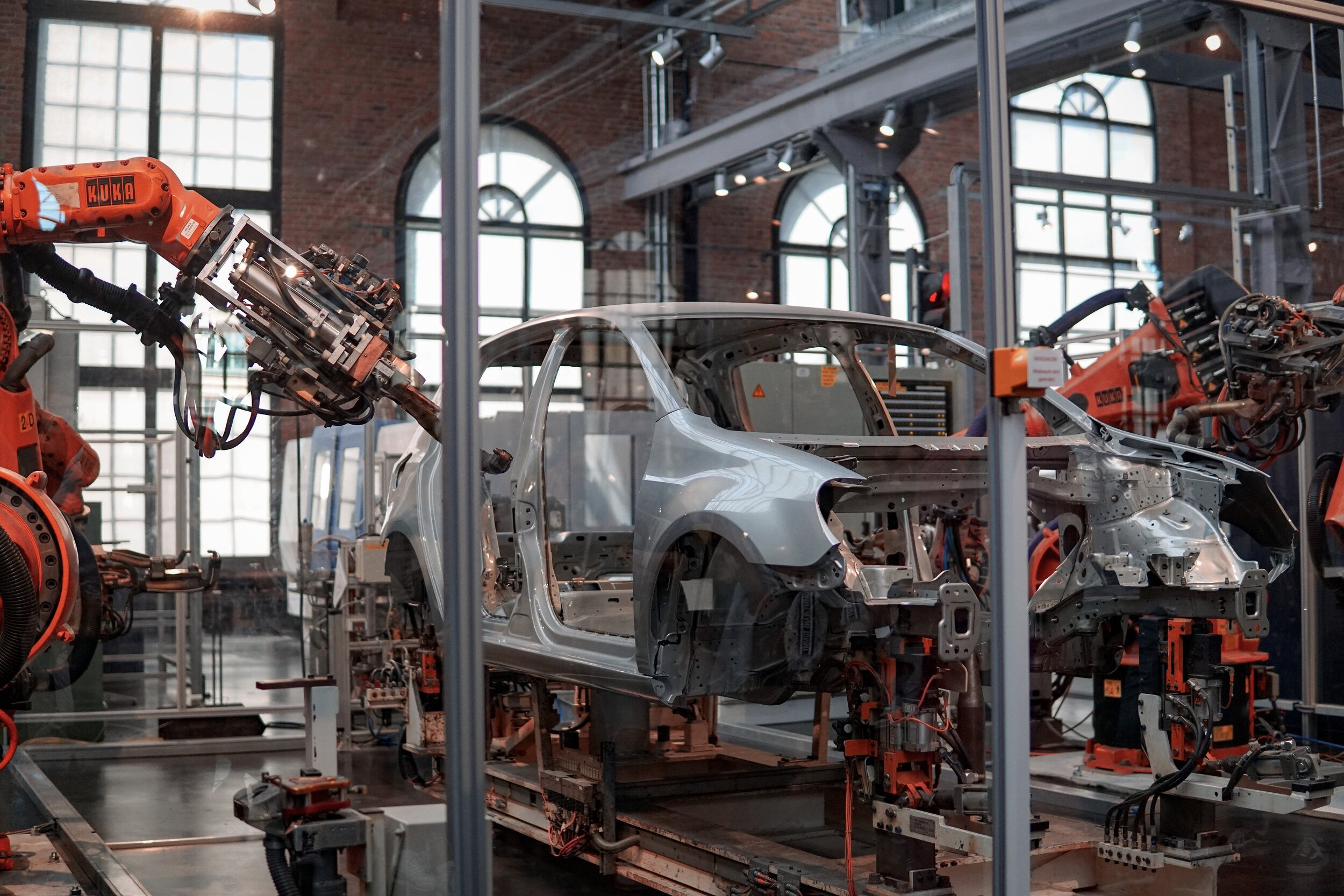
LANGUAGE OF LEAN
Pacemaker
"Pacemaker" is a term commonly used in the manufacturing industry to describe a production process that sets the pace for the rest of the production line. Sometimes also considered as bottleneck station.
"Pacemaker" is a term commonly used in the manufacturing industry to describe a production process that sets the pace for the rest of the production line. A pacemaker process is the one that determines the speed and flow of the entire production process, and therefore has a significant impact on the efficiency and productivity of the manufacturing operation. As a Lean Management Expert, it is important to understand the role and significance of a pacemaker in manufacturing, and how to effectively implement this principle for maximum efficiency and profitability.
The concept of a pacemaker process has its roots in the Toyota Production System (TPS), which is the foundation of the Lean Manufacturing philosophy. TPS emphasizes the importance of flow and standardization in manufacturing, and the pacemaker process is a key component in achieving these goals. The pacemaker process is the first step in the production line and sets the standard for the rest of the processes to follow. This means that the pace, efficiency, and quality of the pacemaker process have a direct impact on the entire production line.
In order to effectively implement the pacemaker principle, it is important to carefully select the appropriate process to serve as the pacemaker. This process should be stable, consistent, and capable of producing high-quality products in a timely manner. It is also important to standardize the pacemaker process to ensure that it runs smoothly and consistently, and that the production line can respond to changes in demand or other factors.
Once the pacemaker process has been established, it is important to monitor and measure its performance regularly. This can be done through the use of Key Performance Indicators (KPIs), such as cycle time, quality rate, and productivity. By monitoring these KPIs, it is possible to identify areas for improvement and to make changes to the pacemaker process or the rest of the production line to improve overall efficiency.
In addition to setting the pace for the production line, a pacemaker process can also have a positive impact on the morale of the manufacturing workforce. When employees see that their efforts are making a significant impact on the overall efficiency and success of the operation, they are more likely to be motivated and engaged in their work.
In a nutshell, the pacemaker principle is a key component of the Lean Manufacturing philosophy, and a valuable tool for Lean Management Experts looking to improve the efficiency and profitability of their manufacturing operations. By carefully selecting the pacemaker process, standardizing its performance, monitoring its performance regularly, and using KPIs to track progress, it is possible to achieve maximum efficiency and profitability in the manufacturing industry.
Cell Production
Cell Production focuses on optimizing the flow of work and improving efficiency in manufacturing and operations.
Cell Production focuses on optimizing the flow of work and improving efficiency in manufacturing and operations. It is based on the concept of organizing work into cells, which are self-contained units responsible for performing a specific set of tasks. The goal of cell production is to minimize waste, increase flexibility, and improve overall performance.
The origins of cell production can be traced back to the 1950s and 60s, when Toyota and other Japanese companies were experimenting with new approaches to manufacturing. Over time, the concept of cell production has evolved and been refined, and today it is widely used in a variety of industries, including automotive, electronics, and consumer goods.
In order to implement cell production effectively, there are several key steps that organizations must take. Firstly, it is important to conduct a thorough analysis of the current state of the manufacturing or operations process, in order to identify areas where improvements can be made. This may involve mapping out the flow of work and identifying bottlenecks or other inefficiencies.
Once these areas have been identified, the next step is to reorganize the work into cells, taking into account the specific requirements of each cell and the skills and expertise of the employees who will be working in them. This may involve rearranging physical work spaces, or changing the way that work is assigned and managed.
It is also important to establish clear communication and feedback mechanisms, so that employees and teams can work together effectively. This may involve setting up regular meetings to discuss performance, or implementing systems for tracking and reporting on key metrics.
In order to ensure a successful implementation of cell production, it is also important to provide training and support for employees. This may involve providing training on the new processes and procedures, or offering coaching and mentoring to help employees develop the skills and knowledge they need to be effective.
Another key aspect of cell production is continuous improvement. This involves regularly reviewing performance and making adjustments as needed, in order to optimize efficiency and reduce waste. This may involve experimenting with different approaches, such as implementing new technologies or streamlining processes, in order to find the best solutions.
In conclusion, cell production is a powerful methodology for optimizing performance in operations and manufacturing. By reorganizing work into cells, minimizing waste, and continuously improving performance, organizations can increase efficiency, reduce costs, and improve overall performance. In order to be successful, organizations must take a structured and systematic approach, and be committed to ongoing improvement.
Bottleneck
Bottlenecks are the pacemaker of your process chain.
Bottlenecks in your process are the pacemakers of existing processes. These means if you tackle your bottlenecks in your process chain, it will have a direct impact on your cash flow.
A Bottleneck in a process chain requires the longest lead time of operations, A typical indicator for a bottleneck station is a upstream increased inventory or Work in Progress. The bottleneck is therefore the weakest link in the chain.
If you are running improvement or KAIZEN Workshops on your bottleneck station the upstream or downstream process steps will never be above 100% of performance. If so the bottleneck station changed to a different process step.
Bottlenecks are great to improve!
The potential of removing bottlenecks is unbelievable high, if you miss the chance to tackle the potential of bottlenecks in order to increase your throughput you are missing the chance to increase your performance and exceed customer demand/expectations. It is quite simple – the cost per hour of a bottleneck station can be seen as the loss of one hour of your complete process chain (e.g. production line) incl. the loss of parts not produced.
The whole deal is about increasing the throughput of your assembly line, to use machines efficiently combined with optimized operator working steps to increase the profitability of the assembly in total. Don’t make the mistake and focus only on the cost reduction part of it think and don’t be fooled by thinking in partial optimization.
To bring it to the point: In manufacturing, bottlenecks are continuously slowing down the whole assembly line. Focusing on permanent existing bottlenecks will sustainable improve the performance of the whole process chain and effect even other areas.
Stay Connected
Ad
We want information fast and in a nutshell. We from OI recommend Blinkist* - because it’s simply the best.
* = Affiliate Link