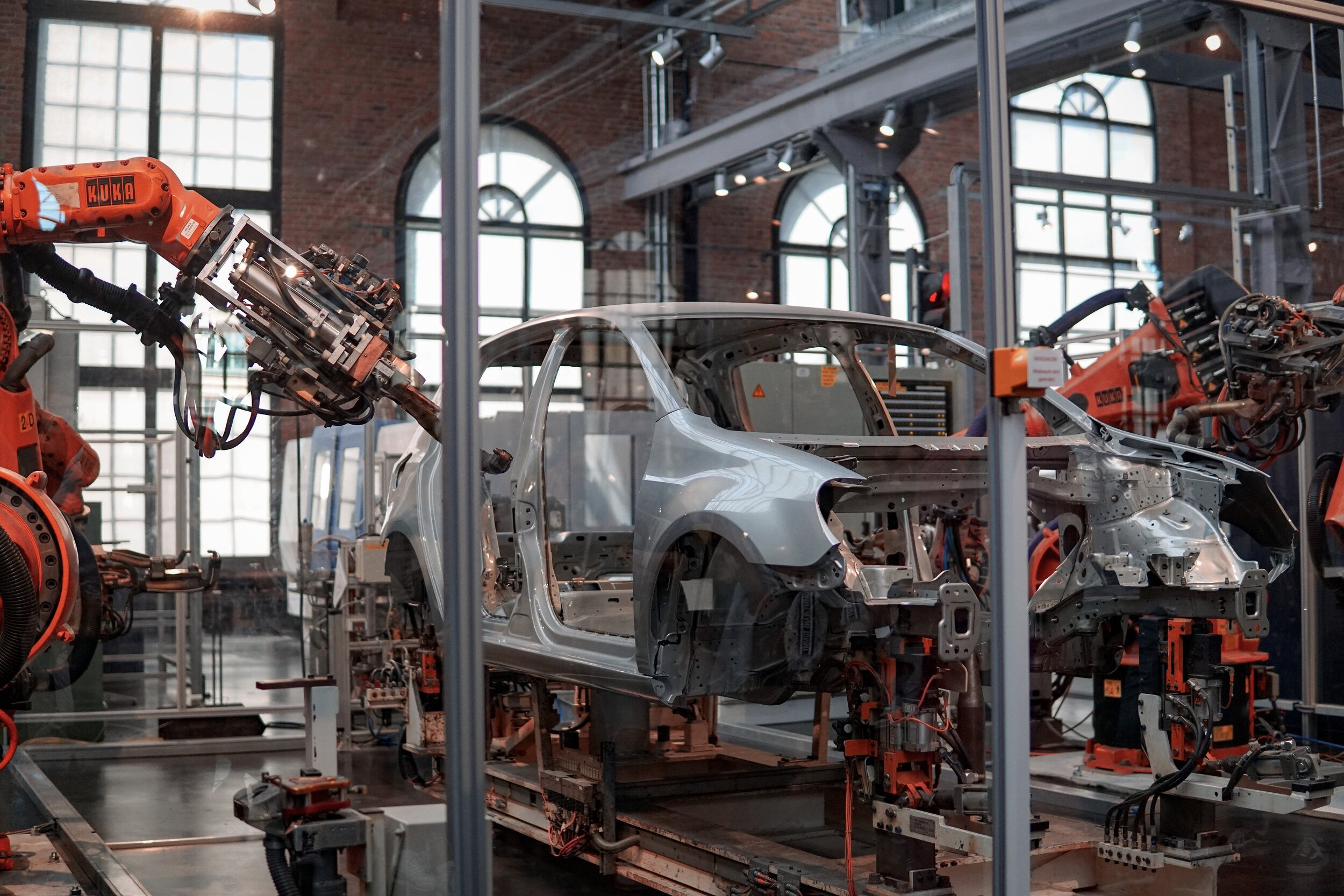
LANGUAGE OF LEAN
SIPOC
SIPOC can be used to clearly define process steps within a process chain.
SIPOC is a > Six Sigma tool that summarizes an entire process at the start of an improvement project. SIPOC can be used to clearly identify process steps within a process chain. A SIPOC diagram is only a snapshot of a process. Each of the letters in SIPOC represent the names of the columns in the table:
S – Supplier, I – Inputs, P – Process, O – Output, C – Customer.
The SIPOC method has its origins in Six-Sigma and is used there in the definition phase of a project. To have it summarized see the following Infographic:
By applying this method, it is possible to quickly gain an overview of all the main elements of a process to be examined, even before more in-depth details are worked out.
SIPOC is a very simple and at the same time very effective method that can also be used in various situations in the lean management context.
Possible applications of a SIPOC can be:
Starting a KAIZEN workshop in order to create a common basic understanding.
To achieve a quick overview (top level) for subsequent process optimization
Simple type of documentation for existing processes
Identification of important process participants (who must attend the KAIZEN workshop)
Definition of the process steps to be investigated within a process chain
How to use SIPOC:
The SIPOC method can be used in many different forms, such as Excel spreadsheets, handwritten tables on flip charts or brownpaper versions using cards or post-it notes.
The easiest way is to start by listing the process steps. No more than 5-7 process steps should be listed, since the SIPOC method is not about carrying out a detailed process analysis, but only about gaining a rough overview.
It often makes sense to note down on the process card those departments or persons who carry out the process for the respective process steps, so that it can be recognized immediately who is responsible for the process.
Input: which input factors are necessary to perform the process step? This could be material, information, machines or a service.
Supplier: who provides these input factors? Do they come from an external supplier or from an internal supplier - perhaps as the output of a previous process step in the process chain?
Output: what is produced as a result in the respective process step. These can be material things such as components, assemblies or finished products, or intangible things such as processed information in the form of a document - e.g. a static calculation or an order confirmation.
Customer: for whom the result was actually produced. Make a distinction between external and internal customers. If no customer is found for the output size, it must be checked whether the process step makes sense at all.
6R
6R - The right product at, the right time, at the right place, in the right quantity, in the right quality and for the right price.
Let’s have a look on the logistics in operation. Everybody crossing the way with logistics will hear about the famous 6Rs the “six right ones” they say.
The right components
in the right amount
at the right place
in the right quality
at the right costs
at the right time
To summarize logistics this is it. The 6 Rs show that the main task of logistics is to make material/goods/components available.
You might have heard about the 7th R > the right customer.
So we think 6R are perfectly known as they got taught for decades. But with the lean transformation all over the 7th R becomes key on hitting lean mindset in logistics. It is all about customer centric orientation of the complete supply chain. It doesn’t matter where, how and why in the end you have to start with your customer and build along the upstream your logistics set up.
And here is the most valuable point, your customers are not only outside your organization, they are among your complete organization. If everyone along the process chain sees the next step as a customer, they also have to meet the customer expectations. This gives you a great pull effect throughout the complete process chain and in addition every employee is responsible as supplier and customer, two roles in one person. With this continuous focus on the customers demand or needs, all signs from the market result in a kind of resonance throughout your complete organization and causes an effect.
Logistics made up his way from simple material supply over optimizing material flow to become a crucial part of operations. Nowadays logistics are the arteries of manufacturing industries.
The traditional way to see logistics is seen in the 6R’s as shown in the beginning. For most of the business cases the 6R’s are enough and suitable in practice. But for real operational excellence and an impact on your lean journey keep always your customers in mind.
Following the 6(7)R’s will affect 4 main areas of your production system
Smoothed production
Warehouse organization
Production synchronous material flow
Cell production
Stay Connected
Ad
We want information fast and in a nutshell. We from OI recommend Blinkist* - because it’s simply the best.
* = Affiliate Link