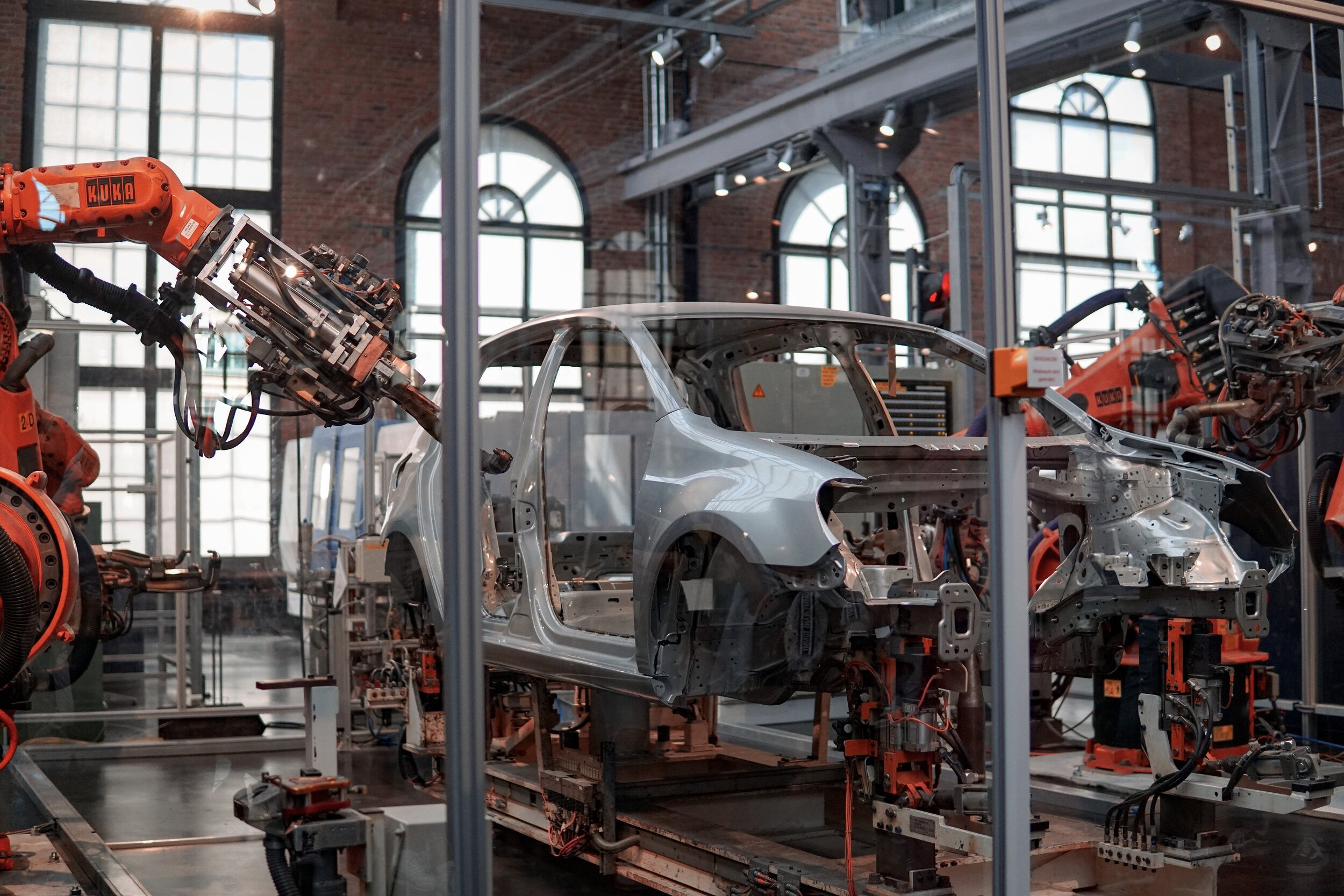
LANGUAGE OF LEAN
Mura
A traditional general Japanese term for unevenness. It is the waste of variation in the production process.
Mura, one of the three types of waste in the Toyota Production System, translates to "unevenness" or "inconsistency" in English. It refers to the irregularity in the flow of work, causing fluctuations in capacity and production. Identifying and removing Mura is essential for creating a steady work pace and optimizing resources.
One of the main causes of Mura is multitasking. When team members are constantly switching between tasks, they often lose focus and efficiency, leading to unevenness in the workflow. This results in longer lead times, increased inventory, and higher costs.
Another cause of Mura is overproduction. Producing more than what is needed, whether it's goods or services, creates an imbalance in the system and results in unnecessary inventory. This not only ties up valuable resources but also increases the risk of defects and rework.
To handle Mura, one must first understand the root cause of the unevenness. This can be done through value stream mapping, a tool that visually represents the flow of work and helps identify areas of waste. By analyzing the current state of the process, one can identify the steps that are causing Mura and implement solutions to eliminate them.
One effective solution is to implement a pull system, also known as "kanban" in Japanese. This system ensures that work is only produced when it is needed, eliminating overproduction and promoting a steady flow of work.
Another solution is to implement standard work. By standardizing the work process, team members are able to work consistently and efficiently, resulting in less Mura. This also helps in identifying and addressing any abnormalities that may occur in the process.
Additionally, involving the team members in problem-solving and continuous improvement activities can lead to increased ownership and accountability, leading to a reduction in Mura.
Implementing a pull system, standard work and involving team members in problem-solving and continuous improvement activities can help organizations to create a steady flow of work and optimize resources.
It's important to note that Mura is not a problem that can be solved once and for all. It's a continuous effort and requires constant monitoring and improvement. Regularly conducting value stream mapping and Gemba walks, where one goes to the place where the work is done to observe and understand the process, can help in identifying and addressing Mura.
In conclusion, Mura is a key concept in lean management and must be addressed to ensure a steady work pace and optimize resources. By understanding the root cause of Mura and implementing solutions such as pull systems, standard work, and involving team members in problem-solving and continuous improvement activities, organizations can achieve the goal of smooth and well-organized workflow.
JIDOKA
Jidoka is the Japanese word for automation. It describes a form of automation where machinery stops by itself when defects are detected and notifies humans to clarify what is going wrong.
JIDOKA - the Japanese term meaning automation. In this form of automation the machinery itself is checking the parts produced for defects after processing. With this constant checking of process quality deviations can be directly detected and when defects occur the complete process is automatically stopped until the problem is solved.
You might have come across the word autonomation, which is simply a combination of the words autonomous and automation that describes the automation with still human interactions. JIDOKA has to be seen as a manufacturing principle rather than a methodology. The idea behind JIDOKA is that all machines in the process chain can run without a dedicated operator checking for process stability and quality outcome. If there is a defect or non-conformity of the process, the machine shuts itself down, preventing the defective parts of getting passed on the downstream process steps and for this reason it prevents producing scrap.
In the Toyota Production System, autonomation is one of the main pillar and is also known as intelligent automation as it is firstly focusing on the quality and the ability of a self running system rather than just focusing on the output. You might have also heard the description of automation with a human touch - if a deviation occurs the machine itself will stop the complete manufacturing process and only with the interaction of an operator, after the problem is solved, it can continue production. The upside is pretty clear - you will not produce any defective parts or waste value adding activities on non-conforming components.
With the use of the JIDOKA principle a number of advantages are coming with it:
Processing of non-conforming parts is immediately noticed, so that neither scrap nor rework occurs. Furthermore, no defective parts are passed on to the downstream processes steps
Since the defects are detected automatically, a 100% end of line inspection is no longer needed within the scope of quality assurance
With the help of automatic error detection, operators are no longer needed to monitor machinery, which is no-value adding activity anyway, so it can be declared as waste in the form of waiting time
Operators have now the freedom to perform multiple tasks during the same time or are able to dedicate themselves to new tasks at all
Maintenance activities will also decrease as crashes or malfunction due to the passing on of non-conforming parts is avoided
JIDOKA is the basis of analyzing the root cause of failures and implement sustainable counter measures to avoid these of occurring again
Stay Connected
Ad
We want information fast and in a nutshell. We from OI recommend Blinkist* - because it’s simply the best.
* = Affiliate Link