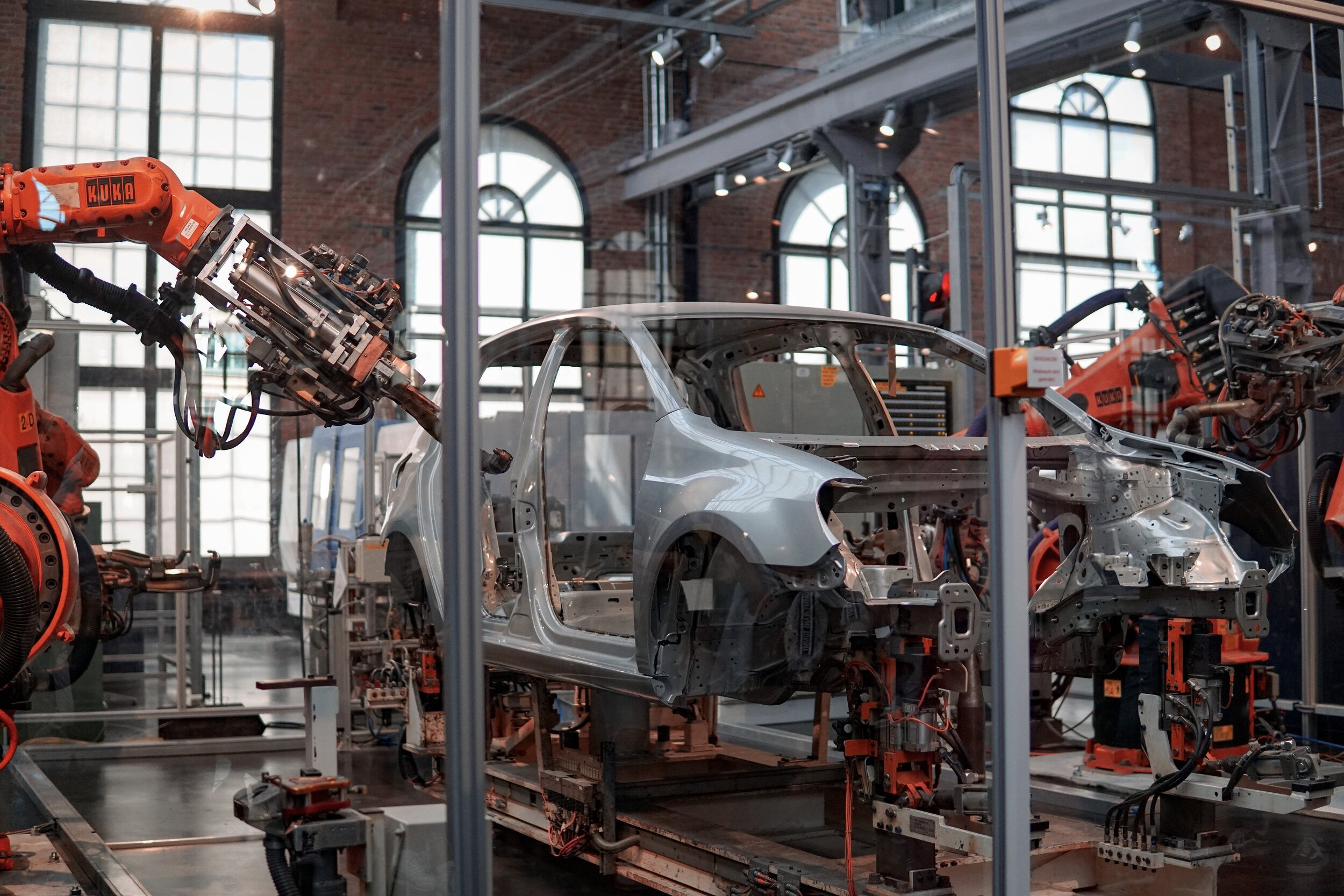
LANGUAGE OF LEAN
Mura
A traditional general Japanese term for unevenness. It is the waste of variation in the production process.
Mura, one of the three types of waste in the Toyota Production System, translates to "unevenness" or "inconsistency" in English. It refers to the irregularity in the flow of work, causing fluctuations in capacity and production. Identifying and removing Mura is essential for creating a steady work pace and optimizing resources.
One of the main causes of Mura is multitasking. When team members are constantly switching between tasks, they often lose focus and efficiency, leading to unevenness in the workflow. This results in longer lead times, increased inventory, and higher costs.
Another cause of Mura is overproduction. Producing more than what is needed, whether it's goods or services, creates an imbalance in the system and results in unnecessary inventory. This not only ties up valuable resources but also increases the risk of defects and rework.
To handle Mura, one must first understand the root cause of the unevenness. This can be done through value stream mapping, a tool that visually represents the flow of work and helps identify areas of waste. By analyzing the current state of the process, one can identify the steps that are causing Mura and implement solutions to eliminate them.
One effective solution is to implement a pull system, also known as "kanban" in Japanese. This system ensures that work is only produced when it is needed, eliminating overproduction and promoting a steady flow of work.
Another solution is to implement standard work. By standardizing the work process, team members are able to work consistently and efficiently, resulting in less Mura. This also helps in identifying and addressing any abnormalities that may occur in the process.
Additionally, involving the team members in problem-solving and continuous improvement activities can lead to increased ownership and accountability, leading to a reduction in Mura.
Implementing a pull system, standard work and involving team members in problem-solving and continuous improvement activities can help organizations to create a steady flow of work and optimize resources.
It's important to note that Mura is not a problem that can be solved once and for all. It's a continuous effort and requires constant monitoring and improvement. Regularly conducting value stream mapping and Gemba walks, where one goes to the place where the work is done to observe and understand the process, can help in identifying and addressing Mura.
In conclusion, Mura is a key concept in lean management and must be addressed to ensure a steady work pace and optimize resources. By understanding the root cause of Mura and implementing solutions such as pull systems, standard work, and involving team members in problem-solving and continuous improvement activities, organizations can achieve the goal of smooth and well-organized workflow.
Implementation of 5S
The 5S Method is a five-level system for the provision of safety, cleanliness and orderliness on the workplace.
If you want the short version just go here. Otherwise we will deep dive in this article on how to implement the 5S methodology in your organization. We will simply follow the 5 Steps and explain the topics.
1st S SEIRI = Sort out all unnecessary objects
Unnecessary objects are all objects that are not needed for the current manufacturing processes (production, logistics, quality, and administration, etc.), that means, defective parts, unused material, material that has been written-off, all spare parts, non-utilized tables and so on
Determine in advance, what is truly needed. This is helpful when dealing with statements such as: “That still can be used“, “That should be useful for something,“ etc.
Remove all redundant objects or at least visually mark them so that everybody is aware that they are to be disposed of
Unused objects should be concentrated in one marked closed area. The decision about those that can not be immediately liquidated, as whether to dispose of them, should be made by the person responsible within 2 weeks
Target: At the workplace are only objects essential for the current work in progress.
Red Tag Campaign
Ask three questions for each separate object:
Is this object useful?
How many of these objects do we need?
Where should this object be stored?
Don‘t support others in searching for excuses. Be fair – mark objects that should be removed in all divisions of the company
Don‘t compromise! When in doubt - the rule applies: Get rid of it!
If there are suggestions for improvement of the current manufacturing process, it is possible to “red tag“ even objects still in use
Make sure that everybody understands what should be marked and why
Course of action and rules for the “Red Tag Campaign”
Write on the tag why the marked object is not needed (Example: Surplus packing boxes; parts stored in boxes are not used any more)
Contact Information about the person who made the decision that the object is superfluous (name and department)
The person responsible for the object will be informed and their name will be entered on the “Red Tag”, and along with the agreed-upon date of removal (maximum 3 days), the action should be recorded (Example: The employee who recognized that the boxes are not used anymore, will inform the warehouse attendant and will appeal to him to verify if they are really not of use anymore. If it will be discovered that the object is still in use, the “Red Tag” will be removed. (For instance: The warehouse manager finds out that the boxes will be used to store other parts very soon)
If the object will be classified among the superfluous, it must be removed within three days by the person who has the responsibility for this area. (For instance: Redundant storage boxes - person responsible for the warehouse). Afterwards the “Red Tag” can be liquidated
Objects can be “Red Tagged” only in working areas of ones responsibility. The Shift Leader can issue “Red Tags” in the entire area they are responsible for
The “Red Tag” will be filled out by hand and attached to the unwanted object.
Examples of unwanted objects:
1 Defective products
Faulty parts
Rejects
2 Unnecessary objects
Unused empty packaging
Personal objects (on undefined places)
Unneeded assembly sets
Unused material (remaining bundles)
Unused tools, auxiliary and production material
Inventory no longer being used
Surplus of manufactured components
2nd S SEITON = Clean-up and correct arrangement of needed objects
After the removal of all unnecessary objects, remove all uncleanness, as new organization of areas for laying down objects or their storage can start only after everything is clean
Each machine and each tool must have its designated place.
Thoroughly deliberate about where you will store material, tools, and equipment
Use colored markings (for instance stickers) to designate areas, cabinets, shelves, cupboards with shelves, important places, direction of work procedures, etc.
With each object ask three key questions: Where? What? How many?
Permanent storage of objects in
Targets:
A place for each object and each object in its place
Visual control and expedient detection of deviations
Proper storage of all needed objects in the right place. These objects can then be found and used whenever needed
Every thing has its own place and after its use is always returned to its place!
Think about color markings on the floor e.g.:
Yellow = transportation zone
White = raw material
Green = finished goods
Red = closed area/NOK parts
3rd S SEISO = Keeping the workplace tidy so as to achieve the already established standards through 5S
The purpose of the cleaning action is to remove all contamination from the workplace and to maintain it in order.
For this purpose a cleaning schedule will be formulated that will determine what is to be cleaned, with what, and by whom
If you discover any shortcomings or abnormalities during the cleaning process – mark them down
All employees of the workplace / work area will participate in the cleaning process
Keep records of the cleaning process, display visually “Red Tags,” as well as the clean-up time schedule of your workplace. Display results
Define responsibilities with consideration even to the smallest work sections
Be effective. Even a five-minute cleansing action can achieve a lot
Targets:
Cleaner and safer workplace
Achieving the already established standards
Cleanliness
Cleanliness at the workplace must be observed, because a clean workplace is essential towards quality and safety at work
If the workplace is not dirty it is not necessary to clean it
Any kind of uncleanness and any kind of untidiness will be visible thanks to the initiation of a regular cleaning process – for instance, dusting, sweeping, and waste disposal
Continuous usage of equipment
Removal of all uncleanness and untidiness
Prevention of working accidents
Cleanliness means controlling, which implies that when cleaning a certain workplace, also check the state of the machinery, equipment, and working conditions
4th S SEIKETSU – Establishing regulations for work standards
SEIKETSU has the greatest importance of all 5S Steps.
With this 5S Step the main focus is on three aspects:
No unnecessary objects
No messiness and
No uncleanliness
Visual control is the first step towards discipline. The ideal workplace is that with which any eventual problems can be detected at first glance – any corrective measures can be immediately implemented
Use control lists to control the 5S standard and to identify deviations from the defined 5S standards
Conduct 5S audits with consideration to the situation on the individual work place. Attempt to identify deviations from the 5S standards
Ask yourself “follow-up questions”, as for instance: Has the mess been cleaned up immediately? Is it clear who is supposed to do the job? Can the clean-up be done quickly? - and others
Targets:
Securing the adherence to the 5S Standards
Increasing the team responsibility on the work place
Schedule of everyday clean-up
5th S SHITSUKE – Adherence to the Work standards and continuous improvement
Discipline, namely, adherence to work standards is basically a question of personal attitude. For it to be easier, various teaching aids are used, e.g. Courses of the 5S Basics
Use photographs, single-topic lectures, video-programs and presentations
Constructive criticism is the foundation for proper 5S training
Take pictures to document the status quo before and after
The Team Leader functions as an example to the team. During his work he should focus on the goals of 5S, he should strive for a continuous improvement of quality and in this direction aim his training activity also
Define together the measures for improvement and how to realize them.
Regulations are better than criticism and a system is better than regulations
Targets:
Promotion of this know-how in the entire company from top-to-bottom
Well-organized work places that require only the minimum attention
The 3 MU
Muda = waste, Muri = overload, Mura = imbalance. Read more about how to define and eliminate the 3 MUs.
In the lean world it is all about “WASTE ATTACK” > eliminate the 3 MUs. It is the bottom line of all KAIZEN and Lean activities. The 3 Mu come from the Japanese words muri, mura and muda. Muda is the most known as it describes waste and we discuss the 7 kinds of waste in the TIMWOOD article. Just to give you a hint TIMWOOD stand for: transport, inventory, motion, over production, over processing and defective parts. These kinds of waste are easily visible by observing manufacturing processes. It gets a little bit trickier if we talk about the other 2 Mu. Muda you get a straight forward feeling, mura and muri are more hidden.
The best way to explain muri is that you are over stressing a system or process. If you e.g. use a forklift that has a maximum of 500kg and you are transporting 1 ton. Your forklift won’t last long. You are either overstressing or trying to do something that can’t be done. The result of it will be a loss in performance.
Mura is unevenness or variation of processes most of the time a result from muri. You can also compare it in administrative work, if you have too little or too much to do. To stick with the example of the forklift, mura would be having only 200kg to load on the forklift on one transportation and on the next route 1.400kg. The result of this variation may be that you try to load 700kg on each route even this is exceeding the max load. The result of it will be that you have breakdowns, defects, excessive motion and other wastes. In all lean management, whether it is manufacturing, logistics, healthcare or knowledge transfer focuses on getting rid of muri, mura and muda in order to improve performance. If you want to get rid of waste in a sustainable way, you have to go upstream and start looking at how products, services or the work itself is designed. You need Value Designing and Value Engineering in the widest sense of the lean terms.
A simple and easy way to make things visible is the classic GEMBA walk – go to the production and see what crime your designers and engineers have committed. Go Gemba helps you to identify and eliminate wasteful steps in assembly and set preventive measures such as Poka Yoke devices to ensure conformity of your products. If we think of designing work itself we want to achieve a continuous and smooth stream of activities. Having this in mind always helps us to redesign processes, get rid of rework, delays or overengineered process steps. Value Stream Mapping as it is done today and redesigning it to focus on fast, high quality hands-off will result in reduced costs and time to market lead times.
MURI in terms of the designing phase will be visible in the need of long working hours to meet the schedule. You will see that it also comes from MURA because the workload itself is not levelled. Who hasn’t been in the situation that you have a design release and suddenly you are twice as busy as before. In the end MURI and MURA leads to MUDA when we start making failures under the pressure of time, when we start releasing before everything has been fully tested or checked.
In the designing phase or let’s say in the creative phase it is typically hard for employees to judge what is waste and what not. It starts with unclear requirements from the customer, but yes some work needs to be done anyway. That’s one point and another one is the mainstream mindset that design is 100% creative and can’t be standardized or quantified. We all heard about Pareto which tells as that 80% of a project are carry over parts and 20% are individual solutions for the specific project.
Lean Design is more a mental rather than a technical challenge.
Carrying on with the example of lean product development, the focus should be to streamline the routine and repetitive work packages so that there is more time for the individual, creative, value-adding part of the project. To clean out your process standardization of items, design elements, documentation, software used and the wiki of Lessons Learned from other projects are just some methods to apply basic lean principles in the development process.
If you think about decentralization of organizations with a global presence, design teams usually suffer from inefficient processes and inadequate design review meetings. Think about standardization as an organization wide language to communicate. If everybody talks the same language you have transparency which rewards you with more time for the creative part.
Considering the cost of delays in time to market, troubleshooting during launch phase and failure occurrence in the field, the design team should think about the rule of ten according costs of failure.
Lean management is based on continuous improvements (kaizen) based on standards and lean design is no different.
Stay Connected
Ad
We want information fast and in a nutshell. We from OI recommend Blinkist* - because it’s simply the best.
* = Affiliate Link