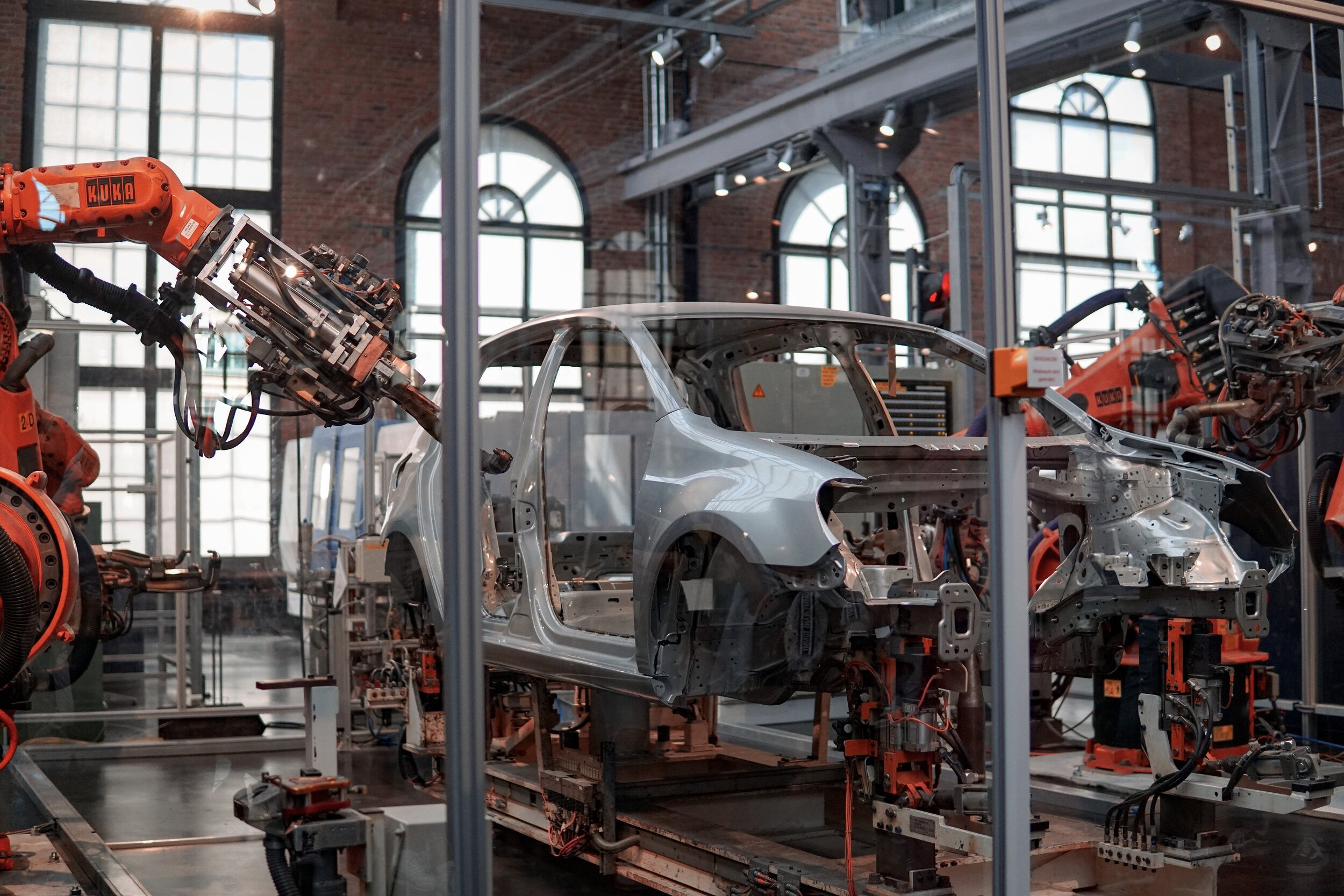
LANGUAGE OF LEAN
One Piece Flow
One-piece-flow is a principle to cut production lead times.
The term One-Piece-Flow basically describes the radical reduction of lead times through flow-optimized production. In an ideal state processed parts or components are moved from one process step to the next without any interim storage. The quantity moved consists only of one part or one batch. You will only be able to achieve this when your work systems are closely connected. The transition of a work system to an one-piece-flow oriented system can only succeed if there is a high availability of existing capacities and flexibility.
Getting your production to flow combines increased productivity and increased employee motivation.
As with most of the lean terms the one-piece-flow principle made its way from the Toyota Production System where it is referred as operator centric work flow. Instead of day in and day out performing the same task at a fixed work station the operator moves with the workpiece through the complete process steps, station after station, for which he/she has to be qualified for all process steps. It is quite similar to a Chaku Chaku line, while Chaku Chaku describes a concrete line layout, one-piece-flow is a principle or mindset so to say. The basic idea behind it is to reduce defects through lacks of concentration and increase motivation of operators through variety.
Lean Manufacturing terms might seem complex, but as most of the time, the principle behind is straight forward and quite simple. As they seem to be no brainers they easily get forget about it which will automatically lead to waste. The best example for waste is the so called TIMWOOD(S), where two main drivers are high amount of Work in Progress (WIP) and high inventories.
Now let us have a look how the One-Piece-Flow principle can help.
The principle of One-Piece-Flow is a new form of flow production. In contrast to conventional forms of flow production the worker in the one-piece.flow production does not remain in his place. Generally speaking the operator has no place of his own - he is always moving with the good. This is exactly where the reference to Chaku-Chaku comes from. With the sequence principle, on the other hand, the operator only interacts with the workpiece on one process step.
After on part is finished the operator starts again at the beginning of the line. This procedure comes with certain demands on the assembly line. U-Shape Layout is the most favorite one, as start and end should be as close as possible to each other in order to keep ways short and transition seamless. The U-Shape Layout is also great as raw material and other components are supplied from the outside, what makes the job of the Mizusumashi easier, and the value adding activities are on the inside.
But speaking about the advantages of One-Piece-Flow, the try to make it short:
Arrangement of workstations simplifies the arrangement of operators
If deviations occur, the operator knows exactly where it is coming from
With the CIP the continuous optimization is really driven on a constant basis
Applied correctly, lead times are drastically reduced
Inventory is drastically reduced
Used space on the shop floor can be reduced by 60% compared to conventional production
Motivation of operators raises as they are responsible from start to end and do not have this monotone daily routine of just one work station
In addition, the use of U-Shaped assembly lines, and if they are build up on standard profiles or standard shelvings, it gives you a huge amount of flexibility. Where workstations or the complete line can be easily extended, reduced or adjusted to new needs.
Push vs Pull Principle
One of the four building blocks of lean production. Push vs Pull production.
The pull principle is one of the main blocks in lean manufacturing > pull manufacturing. The customer demand determines which good will be produced and in which quantity. Max/Min inventory levels are agreed with suppliers and customers. This gives you the opportunity to limit overproduction.
In a pull process a workstation or process step is only being triggered when the downstream processes are free to take the output. This means that only when the customer initiates a need the value adding is started. By this a customer can be seen as internal as well as external one. This is lovely as you make sure that only what you will sell will be produced.
Pull is always to prefer against push. As it allows you to manage the WIP and inventories in between workstations which has a straight impact on your lead time. To successfully install a Pull System you have three choices, it is either the well known continuous flow installed, sequential pull or the replenishment pull.
All three types of connection will help you to achieve different levels of Pull in your environment.
No matter what it always comes down to three factors in your system:
Having max one piece of inventory between two process steps
Having a fix production sequence
and having a max number of parts waiting
Thinking about the three types of a Pull System, the continuous flow system has the highest level of Pull, as all three factors are highly involved. Only One Piece at the time and in between two process steps which means a fixed sequence as well as max one part waiting for the next process step.
If you have several workstation linked in one main manufacturing process working on one final product you have a work cell or simply a production line, depending on the shape you can call it e.g. U-cell.
With the sequential pull system you will have the second best choice of a pull manufacturing. It will have a fixed quantity, the sequence of production is defined but with a max number of WIP allowed between process steps. Basically you will allow buffers in your manufacturing. This can typically be seen in FiFo lines (First in First out).
Last but not least we have a look on the Replenishment Pull. This is in other words your supermarket in the production and your third and last option of implementing pull. The supermarket has a maximum number of components, parts or products waiting to be worked or processed on. But it is not known which one will be next. This type of inventory is usually steered or controlled using the Kanban systematic.
To put it in a nutshell - the following table should be fine to give you an overview:
Stay Connected
Ad
We want information fast and in a nutshell. We from OI recommend Blinkist* - because it’s simply the best.
* = Affiliate Link