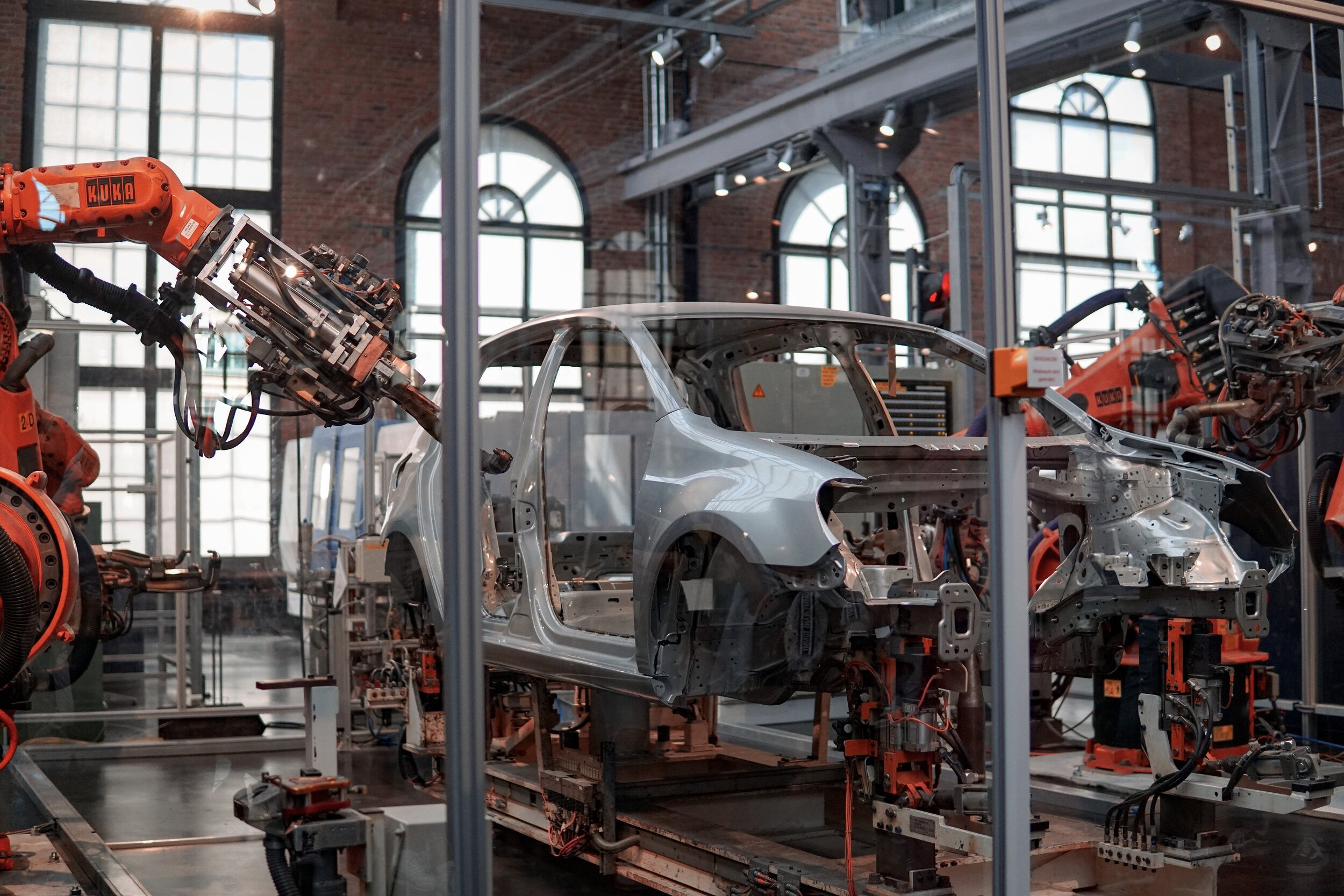
LANGUAGE OF LEAN
Production Smoothing (Heijunka)
Production smoothing, also known as Heijunka, is a key aspect of modern operations management. It refers to the leveling of production to match customer demand, while maximizing efficiency and minimizing waste.
Production smoothing, also known as Heijunka, is a key aspect of modern operations management. It refers to the leveling of production to match customer demand, while maximizing efficiency and minimizing waste. This technique has been proven to be an effective way to manage production processes and increase competitiveness in the marketplace.
The objective of production smoothing is to create a steady flow of products and services, reducing the variability and fluctuations in the production process. This helps to minimize the waste and resources associated with overproduction, excess inventory, and bottlenecks in the production line. By leveling production, companies can better predict customer demand and adjust their production processes accordingly.
One of the primary benefits of production smoothing is the reduction of waste in the production process. By leveling production, it minimizes the need for excess inventory and eliminates the waste associated with overproduction. This helps to minimize the costs associated with storage, handling, and transportation of excess inventory, while improving overall efficiency.
Another advantage of production smoothing is the improvement of customer satisfaction. By better predicting and matching customer demand, companies can ensure that they have the right products and services available at the right time. This helps to build stronger relationships with customers and improves the overall perception of the company.
To implement production smoothing, companies must first understand their customer demand patterns and the production processes that support them. This requires a thorough analysis of the production line, including the identification of bottlenecks and areas of waste. The company should then develop a production plan that balances customer demand with the production processes to create a steady flow of goods and services.
The company should also implement effective communication and collaboration between all departments, including sales, marketing, engineering, and production. This helps to ensure that all processes are aligned and working together towards the common goal of production smoothing. The company should also consider the use of technology and equipment to automate the production process and improve efficiency.
It is also important to engage employees in the production smoothing process. By involving employees in the implementation and ongoing management of production smoothing, companies can tap into their expertise and insights, and build a culture of continuous improvement. Employees should also receive training and development opportunities to enhance their skills and knowledge in production smoothing techniques.
In a nutshell, production smoothing is an effective way to manage production processes and increase competitiveness in the marketplace. By reducing waste, improving customer satisfaction, and engaging employees, companies can create a steady flow of goods and services, and improve their overall production efficiency. By embracing this technique, companies can achieve operational excellence and maintain their competitive edge in the marketplace.
Rapid Improvement Event
Rapid Improvement Events, also known as Kaizen events, are a powerful tool for improving production processes in every industry.
Rapid Improvement Events, also known as Kaizen events, are a powerful tool for improving production processes in the manufacturing industry. They are focused, short-term initiatives aimed at solving specific problems and improving processes in a rapid and efficient manner.
At the heart of a Rapid Improvement Event is the involvement of a cross-functional team of employees, each bringing a unique perspective and skillset to the table. The team works together to identify and solve problems, test new ideas, and implement solutions that can have an immediate impact on the production process.
One of the key benefits of Rapid Improvement Events is the speed with which they can deliver results. By focusing on a specific problem and working together as a team, significant improvements can be made in just a few days or weeks. This can be especially valuable in the manufacturing industry, where time is often of the essence and even small improvements can make a big difference.
To ensure the success of a Rapid Improvement Event, it's important to follow a structured methodology. This typically includes the following steps:
Define the problem and scope of the event. What is the specific issue that needs to be addressed, and what is the desired outcome of the event?
Assemble the cross-functional team. Choose team members who have a strong understanding of the problem and can bring a variety of skills and perspectives to the table.
Conduct a thorough analysis of the problem. Gather data, observe processes, and engage in root cause analysis to understand the underlying cause of the problem.
Develop and implement a plan of action. Based on the findings of the analysis, create a plan of action that addresses the root cause of the problem and implements solutions that will improve the production process.
Implement and monitor the changes. Once the plan of action is in place, implement the changes and monitor the results to ensure they are having the desired impact.
Reflect and celebrate successes. Reflect on the successes of the event and celebrate the improvements that were made.
Rapid Improvement Events are a powerful tool for improving production processes in the manufacturing industry. By bringing together a cross-functional team, focusing on a specific problem, and following a structured methodology, organizations can achieve significant improvements in a short amount of time.
In a nutshell, it is important to embrace a continuous improvement mindset and actively seek out opportunities to improve production processes. Rapid Improvement Events provide a structured and efficient way to do just that, delivering results that can have a lasting impact on an organization's success.
Cellularization
Cellularization is a lean manufacturing methodology that aims to optimize the flow of materials, information, and people within a manufacturing or production environment.
Cellularization is a lean manufacturing methodology that aims to optimize the flow of materials, information, and people within a manufacturing or production environment. Its goal is to create a more efficient, flexible, and responsive production system that can quickly adapt to changing customer demands and market conditions.
The origin of cellularization can be traced back to the early days of the Toyota Production System (TPS), which was developed in the 1950s and 60s. TPS was based on the principles of Just-In-Time (JIT) production and was designed to reduce waste, improve quality, and increase productivity. The concept of cellularization emerged as a way to create small, self-contained production cells that were optimized for specific product families or types of work.
The core idea behind cellularization is to create a flow of work that is highly synchronized and integrated, with minimal inventory and waste. This is achieved by organizing the production environment into cells that are designed to handle specific product families or product types. Each cell is equipped with the necessary tools, equipment, and materials to complete the work in a continuous flow, without the need for batch processing or work-in-progress storage.
Cellularization also requires a cross-functional team approach, where workers from different areas of the organization come together to work on a specific product family or type of work. This team-based approach helps to ensure that everyone has a clear understanding of the work, and it encourages collaboration and communication between different departments.
One of the key benefits of cellularization is that it enables organizations to respond quickly to changes in customer demand and market conditions. For example, if a new product is introduced, the production cell for that product can be quickly reconfigured to accommodate the new work. This agility is a critical advantage in today's fast-paced and highly competitive market.
Another benefit of cellularization is that it promotes continuous improvement. The small, self-contained nature of the cells allows for close observation and monitoring of the work, which in turn enables quick and effective identification and elimination of waste. The cross-functional teams are also empowered to identify and implement improvements that can be made to the production process.
To effectively implement cellularization, organizations need to carefully consider the following factors:
Work flow design: The first step in implementing cellularization is to carefully design the work flow to ensure that it is optimized for the specific product family or type of work being performed.
Equipment selection: The right tools and equipment are critical to the success of cellularization. Organizations need to carefully select the tools and equipment that will be used in each cell, and ensure that they are properly maintained and calibrated.
Cross-functional teams: Teams of workers from different departments must be assembled to work together in each cell. These teams need to be trained on the new work processes, and encouraged to collaborate and communicate effectively.
Lean leadership: Leaders at all levels of the organization need to embrace the principles of lean manufacturing and support the implementation of cellularization. This includes providing the resources, training, and coaching that teams need to succeed.
In a nutshell, cellularization is a powerful and effective methodology for optimizing the flow of materials, information, and people within a manufacturing or production environment. Its success depends on careful design of the work flow, selection of the right tools and equipment, and the development of cross-functional teams. With the right leadership and support, cellularization can help organizations to achieve greater efficiency, flexibility, and responsiveness, and to remain competitive in today's fast-paced and dynamic market
Swim Lane Flowchart
A Swim Lane Flowchart, also known as a cross-functional flowchart, is a type of process mapping tool that is used to visually represent the flow of a process and the various roles and responsibilities involved in that process.
A Swim Lane Flowchart, also known as a cross-functional flowchart, is a type of process mapping tool that is used to visually represent the flow of a process and the various roles and responsibilities involved in that process. The methodology of the Swim Lane Flowchart comes from the field of Lean management and operational excellence, which emphasizes the importance of efficiency and continuous improvement in business operations.
The Swim Lane Flowchart is used to clearly identify and document the steps in a process, as well as the individuals or groups responsible for each step. This allows for a clear understanding of the process and helps to identify areas for improvement. The Swim Lane Flowchart is particularly useful for identifying bottlenecks and delays in a process, as well as for identifying areas where multiple teams or departments are involved in a single process.
One of the key benefits of the Swim Lane Flowchart is that it helps to break down silos and promote cross-functional collaboration. By clearly documenting the roles and responsibilities of different teams and departments, the Swim Lane Flowchart helps to identify areas where different teams can work together more effectively. This can lead to increased efficiency and improved communication among different teams and departments.
Another benefit of the Swim Lane Flowchart is that it helps to identify areas where automation can be used to streamline a process. By clearly documenting the steps in a process and the individuals or groups responsible for each step, the Swim Lane Flowchart can help to identify areas where automation can be used to reduce human error and improve efficiency.
The Swim Lane Flowchart is also useful for identifying areas where standardization can be used to improve a process. By clearly documenting the steps in a process and the individuals or groups responsible for each step, the sSwim Lane Flowchart can help to identify areas where standardization can be used to reduce variation and improve the overall quality of a process.
In conclusion, the Swim Lane Flowchart is a powerful tool for improving business operations and promoting cross-functional collaboration. By clearly documenting the steps in a process and the individuals or groups responsible for each step, the Swim Lane Flowchart can help organizations to identify areas for improvement and take action to improve efficiency and effectiveness. Whether it is used to identify bottlenecks and delays in a process, or to promote automation and standardization, the Swim Lane Flowchart is a valuable tool for organizations that are committed to operational excellence and continuous improvement.
Stay Connected
Ad
We want information fast and in a nutshell. We from OI recommend Blinkist* - because it’s simply the best.
* = Affiliate Link